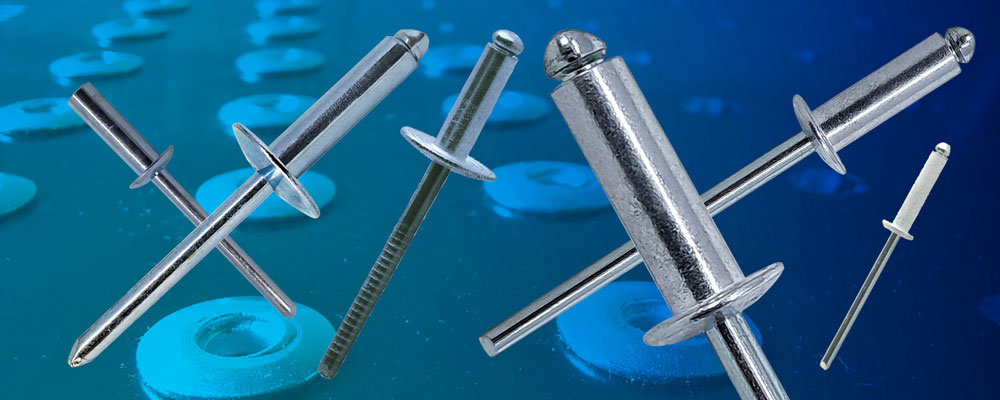
How to Choose the Right Blind Rivet for Every Application
When access to both sides of a workpiece isn’t an option — because maybe there’s a wall, an engine, or just plain bad luck in the way — blind rivets come to the rescue. Choosing the right one isn’t just important; it’s the difference between a clean, professional joint and a future rattling disaster.
Types of Blind Rivets
Blind rivets come in several variations, including standard open-end, closed-end (sealed), multi-grip, and structural types.
Open-end rivets are common for general use where basic strength is sufficient. Closed-end rivets are ideal when waterproofing is required. Multi-grip rivets can accommodate varying material thicknesses, reducing the need for multiple rivet sizes. Structural blind rivets are engineered for heavy-duty applications and provide high shear and tensile strength.
A full guide to Standard and Structural rivets are below:
Material Selection
The rivet material should match or complement the materials being joined. The Scell-it UK range have three main types :
Aluminum rivets are lightweight and corrosion-resistant, perfect for thin metals and non-critical structural work. Easy to set with minimum of tool requirements.
Steel rivets provide superior strength and are used where high loads are expected in non-corrosive environments.
Stainless steel rivets offer excellent corrosion resistance for harsh environments – available in grade A2 or A4.
Sizing Considerations
Proper sizing is crucial for blind rivets. The diameter must match the load requirements, while the grip range must accommodate the total thickness of the materials. A rivet’s length should be sufficient to allow proper expansion and secure fastening without over-compression.
Blind Rivet Head Styles
The head style of a blind rivet affects both the appearance and the performance of the finished joint.
The most common types are domed heads, which offer a standard, all-purpose profile suitable for most applications. Countersunk heads (also called flush heads) sit flush with the material surface, ideal for aerodynamic or aesthetic requirements, such as in automotive or aerospace assemblies.
Large flange heads distribute the load over a broader area, reducing the risk of pull-through in softer or brittle materials like plastics or thin sheet metal.
Choosing the correct head type ensures optimal load distribution, improves the final appearance, and helps meet specific functional needs.
Environmental Factors
In corrosive or wet environments, selecting a stainless steel or coated rivet prevents rust and ensures a long-lasting hold. For applications exposed to vibration, a locking blind rivet can prevent loosening over time.
Conclusion
By carefully selecting the type, material, and size of a blind rivet based on application needs, you can achieve a secure, maintenance-free connection that stands the test of time.
Choosing the right blind rivet isn’t complicated — but it does require a little thought. Get it right, and your project will be rock solid. Get it wrong, and you’ll be revisiting it sooner than you’d like — rivet gun in hand, and regret in your heart.
For more advice or information on your rivet requirements call our experts at Scell-it UK.
continue reading